Safety Precautions for Press Machines
Operating a press machine is no small task.
The sheer power and precision required to form, cut, or shape materials demand the utmost attention to safety. Adhering to essential safety precautions prevents accidents and ensures your operations run smoothly and without costly interruptions.
Understanding Press Machine Hazards
Recognizing the risks associated with press machines is crucial for maintaining a safe work environment.
Common Risks
When working with press machines, understanding the potential hazards is the first step toward prevention. Common risks include:
- Pinch Points: These occur when two parts move together, creating a hazard for fingers, hands, or other body parts.
- Ejection of Materials: High-force operations can lead to materials being ejected unexpectedly, posing a risk to operators and bystanders.
- Mechanical Failures: Even the most well-maintained machines can experience mechanical issues that could lead to dangerous situations if not properly addressed.
Potential Consequences
The consequences of overlooking these risks can be severe. Injuries from press machines can range from minor cuts and bruises to more serious injuries, such as fractures, amputations, or even fatalities.
Additionally, mechanical failures can lead to extensive damage to the machine and significant downtime, affecting productivity and profitability.
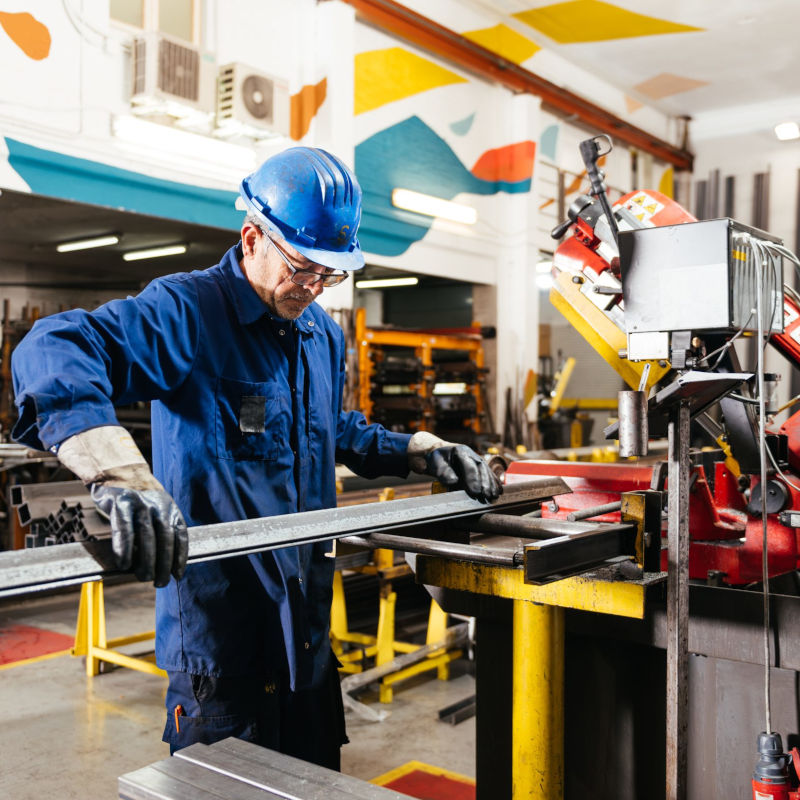
Essential Safety Features of Press Machines
Equipping press machines with the right safety features is vital to protecting operators and maintaining a secure work environment.
Safety Guards
Safety guards are your first line of defense against accidental contact with moving parts. These barriers prevent operators from getting too close to dangerous areas of the machine, such as the die area or other moving components, reducing the risk of injury.
Emergency Stop Buttons
In an emergency, every second counts. Easily accessible emergency stop buttons are crucial for quickly halting operations and preventing accidents.
These buttons are strategically placed so that they can be quickly reached by operators, ensuring that the machine can be stopped immediately if something goes wrong.
Overload Protection
Overload protection systems are designed to prevent the press machine from operating beyond its capacity. These systems automatically stop the press if it detects a potential overload, protecting both the machine and the operator from harm.
Best Practices for Safe Operation
Adhering to best practices for operating press machines is essential for minimizing risks and ensuring a safe work environment.
Proper Training and Certification
Operating a press machine requires specialized knowledge and skills. Ensuring that all operators are properly trained and certified is essential for safe operation.
Proper training teaches operators how to use the machine, recognize potential hazards, and take appropriate action to avoid them.
Regular Maintenance and Inspections
Routine maintenance and safety inspections are critical to keeping your press machine in optimal working condition. Regular inspections help identify wear and tear, allowing for timely repairs or replacements before a malfunction occurs. A well-maintained machine is not only safer but also more efficient. Maintenance for hydraulic presses ensures that all components are functioning correctly, reducing downtime and extending the life of the equipment.
Personal Protective Equipment (PPE)
Personal Protective Equipment (PPE) is a must for press machine operators. Essential PPE includes safety glasses to protect against flying debris, gloves to safeguard hands from sharp edges, and steel-toed boots to prevent foot injuries.
Wearing the appropriate PPE significantly reduces the risk of injury during operation.
Operating Procedures to Enhance Safety
Implementing proper operating procedures is key to preventing accidents and ensuring a safe work environment.
Pre-Operation Checks
Before starting the press machine, conducting thorough pre-operation checks is a crucial step. This involves inspecting the machine for any signs of wear or damage and ensuring all safety features, such as guards and emergency stop buttons, are functional. These checks help prevent accidents before they happen.
Safe Loading and Unloading
Properly loading and unloading materials is key to preventing accidents. Always follow guidelines for the safe handling of materials, ensuring they are securely positioned before the operation begins. This reduces the risk of materials being ejected or causing other issues during operation.
Monitoring During Operation
Continuous monitoring during machine operation is essential. Keeping a close eye on the machine and its operation can help you quickly address any issues or abnormalities that arise, preventing potential accidents and ensuring the process runs smoothly.
Emergency Response Protocols
Having a clear and effective emergency response plan is critical in minimizing the impact of accidents when they occur.
Accident Response
In the unfortunate event of an accident, knowing the correct response is vital. Immediate steps include stopping the machine, administering first aid, and contacting emergency services if necessary. Quick and effective responses can mitigate the severity of injuries and prevent further harm.
Reporting and Documentation
After an incident, it’s important to report it to the relevant authorities and document all details for safety compliance. This documentation is not only crucial for regulatory purposes but also helps in identifying the root cause of the incident, allowing for the implementation of preventive measures.
Creating a Safety-First Culture
Cultivating a safety-first culture within your organization is essential for maintaining a safe and productive workplace.
Regular Safety Training
Safety doesn’t end with initial training. Regular safety training sessions ensure that all employees are up-to-date with the latest best practices and safety protocols. This continuous education helps reinforce the importance of safety and keeps safety procedures fresh in the minds of all operators.
Encouraging Communication
A safety-first culture thrives on open communication. Encourage employees to speak up about any safety concerns or suggestions for improvements. By fostering an environment where safety is prioritized, everyone is more likely to adhere to safety protocols and contribute to a safer workplace.
Safety Audits and Improvements
Regular safety audits are an effective way to identify potential hazards and areas for improvement. Continuously seeking ways to enhance safety protocols and equipment can help you create an environment where safety is always at the forefront of operations.
Magnum Press’s Commitment to Safety
At Magnum Press, safety is a top priority in the design and operation of our hydraulic presses.
Built-In Safety Features
At Magnum Press, we take safety seriously. Our machines come equipped with advanced safety features designed to protect operators and ensure safe operation. From safety guards to overload protection systems, every machine is built with your safety in mind.
Customer Support and Training
We don’t just provide machines; we provide the support and training needed to operate them safely. Our comprehensive training programs and ongoing customer support ensure that you have the knowledge and resources to maintain a safe working environment.
Industry Standards and Compliance
Magnum Press is committed to meeting and exceeding industry safety standards. Our machines comply with all relevant regulations, giving you peace of mind that you’re operating within the highest safety guidelines.
Prioritize Safety with Magnum Press
Don’t leave safety to chance. Contact Magnum Press today to learn more about our safety features, and training programs, or to schedule a consultation. Let’s work together to create a safer, more efficient workspace.
Reach out to us via our easy-to-use inquiry form or call us directly at (855) 498-7077 to discuss how we can help you prioritize safety in your operations.