Essential Hydraulic Press Safety Tips for a Safer Workspace
Hydraulic presses power industries like automotive, food processing, and aerospace, but safety must always be a priority in their use. Beyond the financial costs of accidents – such as medical bills, lost productivity, and equipment repairs – the well-being of your team is at stake. Injuries not only harm employees physically but can also lower morale, creating a lasting sense of unease and danger in the workplace.
This environment can hinder performance and teamwork, making it essential to foster a culture of safety and making sure everyone understands the potential hazards and performs safety protocols associated with hydraulic presses. Explore with Magnum Press how prioritizing safety in hydraulic press operations can protect your team, maintain productivity, and create a more secure workplace.
Train Hydraulic Press Operators and Everyone in the Workspace Properly
Proper training is crucial in maintaining a safe workplace when operating hydraulic presses. Comprehensive, ongoing training should be provided to both operators and anyone working near the machines.
Understanding how the press works, potential risk, and safety procedures allows everyone to recognize dangers and respond effectively during emergencies.
Operators must undergo hands-on instruction covering safe operations, safety features, and emergency protocols before using the equipment. They must also take refresher courses once or twice a year, or when the equipment is upgraded, new safety regulations are introduced, an incident occurs, or an employee returns after an extended period of time off.
Make Sure Everyone Understands the Hazards That Hydraulic Presses Present
While comprehensive training helps in teaching safe operation, it’s equally important for everyone in the workspace to understand the specific hazards posed by hydraulic presses. Awareness of these dangers goes beyond ensuring safe and proper use of the equipment.
It helps everyone in the workplace recognize potential risks in their surroundings, which enables them to alert the operator or supervisor, stay clear of the danger zone, report the issue, activate emergency stop systems, or assist in emergency situations.
By understanding the consequences of accidents involving hydraulic presses, everyone is more likely to remain vigilant, act responsibly, and consistently follow safety protocols. This collective awareness and mindset fosters a safer environment, where the entire team works together to prevent incidents and safeguard each other.
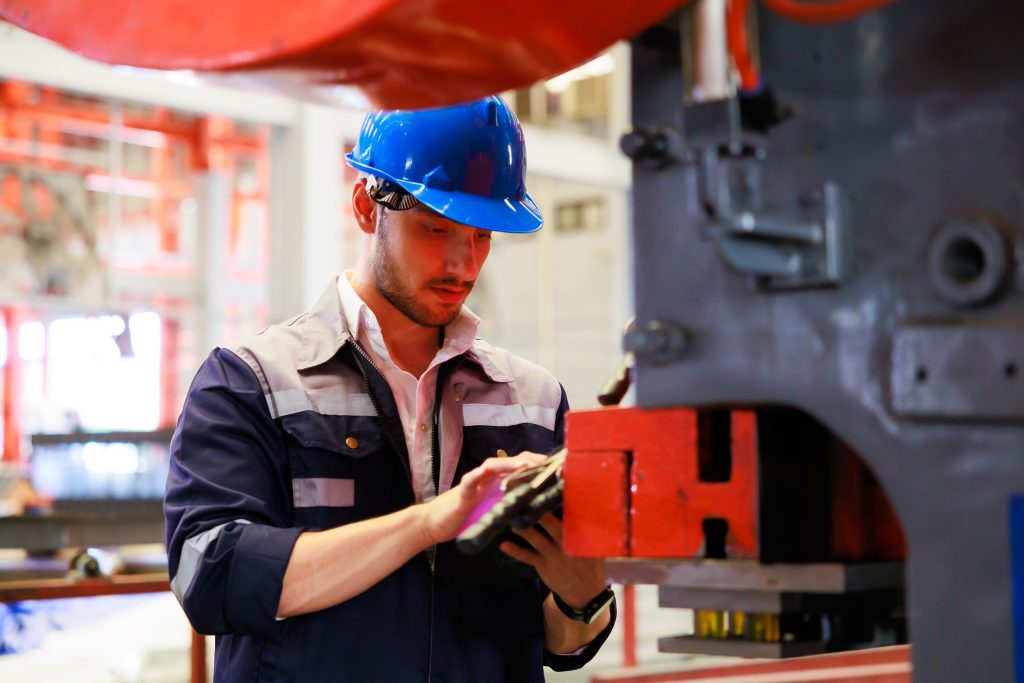
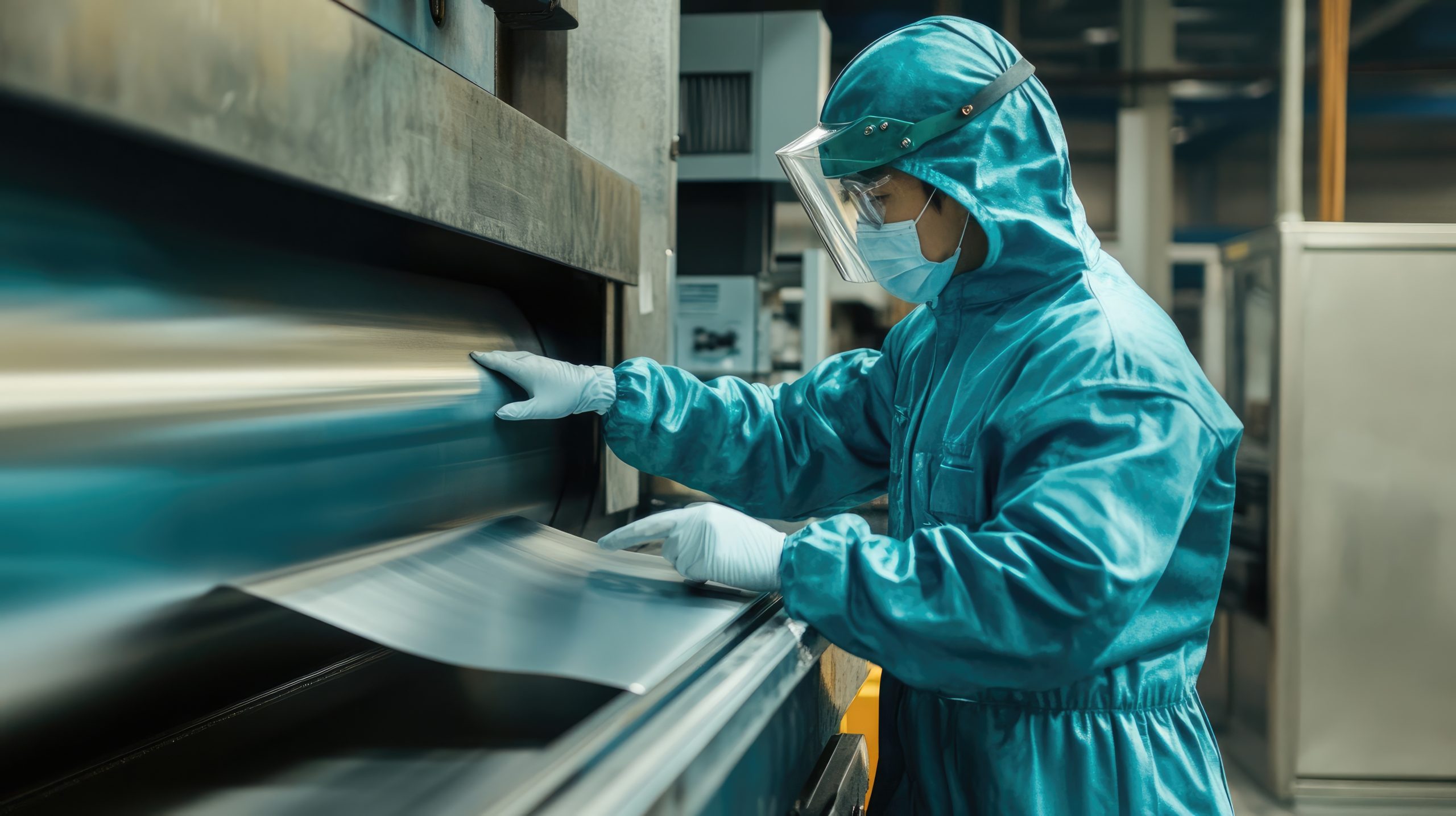
Ensure Proper Use of Personal Protective Equipment (PPE) on the Production Floor
Personal protective equipment (PPE) is essential for safeguarding workers from injuries when operating or working near hydraulic presses. It’s critical that everyone on the production floor consistently wears their PPE, including safety glasses, gloves, steel-toed boots, hearing protection, and others that may be necessary for handling materials and other items in your operations.
Supervisors should ensure PPE is properly fitted and in good condition at the start and periodically throughout the time of operations. Together with regular reminders through signs on the production floor and important areas, the importance of wearing PPE properly is reinforced, reducing the risk of injuries caused by equipment malfunctions or workplace hazards.
Perform an Inspection Before Operating the Press
Conducting an inspection before operating a hydraulic press is essential for ensuring operator safety and preventing costly malfunctions or production downtimes. Regular checks help identify potential issues early, making repairs simpler and reducing the likelihood of accidents, keeping production on track. Inspections also extend the machine’s lifespan, protecting your business from expensive damage or repairs.
Since not all presses and operations are the same, safety procedures should be tailored specifically to your hydraulic press model and use case. Collaborating with the manufacturer or an industry safety expert is key to developing an effective pre-operation checklist that addresses these unique factors.
Test the Emergency Stop Button Regularly
Although a pre-operation inspection covers testing critical functions like the emergency stop button, it requires special attention in preventing accidents or aggravating ones that have already occurred.
A malfunctioning emergency stop could lead to catastrophic consequences if an unexpected incident occurs. Because of this, testing each emergency stop button in the production floor is essential in ensuring its functionality, which protects both workers and equipment from harm.
Never Tamper with the Machine’s Safety Features
Hydraulic presses are equipped with safety mechanisms like guards, light curtains, and two-hand controls to protect operators and prevent accidents. These features should never be bypassed, disabled, or removed, as each one plays a critical role in minimizing the risk of injury if something goes wrong.
Tampering with or altering these safety features can also lead to dangerous situations that put your workers and equipment at risk. It’s essential that hydraulic press operators understand the importance of these safety features and receive proper training on their use. Without these, they may unknowingly bypass or misuse these features, increasing the risk of harm, malfunction, or equipment damage.
Implement Safe Operating Procedures
Establishing clear, standardized operating procedures is essential for ensuring the safe use of your hydraulic presses. These procedures should cover every aspect of press operation relevant to your production line, including proper material placement, handling press controls, and maintaining safe distances from moving parts.
Standardized guidelines eliminate any guesswork and inconsistencies, reduce the chances of errors during operation, and make it easier to implement improvements for safety and production optimization.
Ensure Operators are Always Mindful of their Workspace and Surroundings
Hydraulic press operators must maintain constant awareness of their surroundings to ensure safety. They should always be vigilant, keeping their hands, fingers, and loose clothing away from moving parts to prevent accidents. And, they should ensure their workspace is clear of obstructions or debris, as these can cause distractions or hazards.
In addition to regular training and refreshers, management plays a role in fostering these behaviors. Supervisors should closely monitor for compliance with safety protocols and correct unsafe practices immediately. Implementing realistic production goals and offering incentive programs for safe behavior can further reduce the temptation to rush, promoting a safer and more mindful work environment.
Perform Regular Maintenance and Keep the Machine in Peak Condition
Regular maintenance is essential for keeping your hydraulic press in peak condition. Routine upkeep, such as lubrication, part replacements, and inspections for wear and tear, helps prevent breakdowns and ensures the machine operates safely and efficiently. Neglecting maintenance can lead to costly malfunctions and increased risks of accidents.
Maintaining a detailed maintenance log is crucial to stay on top of repairs and servicing. This log helps track completed tasks and schedule future upkeep, minimizing downtime and extending the press’s lifespan. A well-maintained press not only protects your workforce from potential hazards but also boosts productivity. For more advice, check out maintenance tips for hydraulic presses.
Be Prepared for Emergencies
Emergency preparedness is critical in workplaces using hydraulic presses. All employees should be familiar with emergency procedures, including how to safely shut down the machine, evacuate the area, and administer first aid. Regular emergency drills are key to ensuring everyone’s preparedness and having a swift response when it becomes necessary.
Management can further enhance preparedness by installing clear communications systems for alerting others of an emergency and assigning safety roles to specific team members.
First aid kits, fire extinguishers, and emergency shut down instructions should be easily accessible and clearly marked. Regular review and update of emergency protocols should be done to adapt to new risks or equipment changes.
Ensure a Safer Workplace with These Essential Hydraulic Press Safety Tips
Prioritizing safety is essential for maintaining a productive injury-free workspace when using hydraulic presses. By implementing the right training, performing regular inspections, and ensuring safety features are never tampered with, you can significantly reduce the risk of accidents.
And, keeping a focus on emergency preparedness and enforcing safe operating procedures further protects both your operators and business.
Safety is a commitment, and by fostering a safety first culture – where everyone understands the hazards and gives importance to following protocols. This results in a more secure, efficient, and productive workspace for everyone involved.
Contact Us for a Quote
Looking for a dependable, high-performance hydraulic press?
Boost safety and productivity with Magnum Press! Contact us at 855-498-7077, or reach out online for a quote on standard models or custom designs tailored to your needs.